As finishing touches are being made on our new Butech Bliss Temper Mill Cut-to-Length Line in our Catoosa, OK facility, it seemed appropriate to take a deeper dive into what exactly a temper mill cut-to-length line is and how it differs from a standard cut-to-length line and a stretcher leveling line.
In the steel industry, achieving high-quality products requires specialized processing techniques. Three important components in this realm are the temper mill cut-to-length line, the standard cut-to-length line, and the stretcher leveling line. While they all play crucial roles in steel processing, each serves distinct functions and yields different outcomes.
Temper Mill Cut-to-Length Line
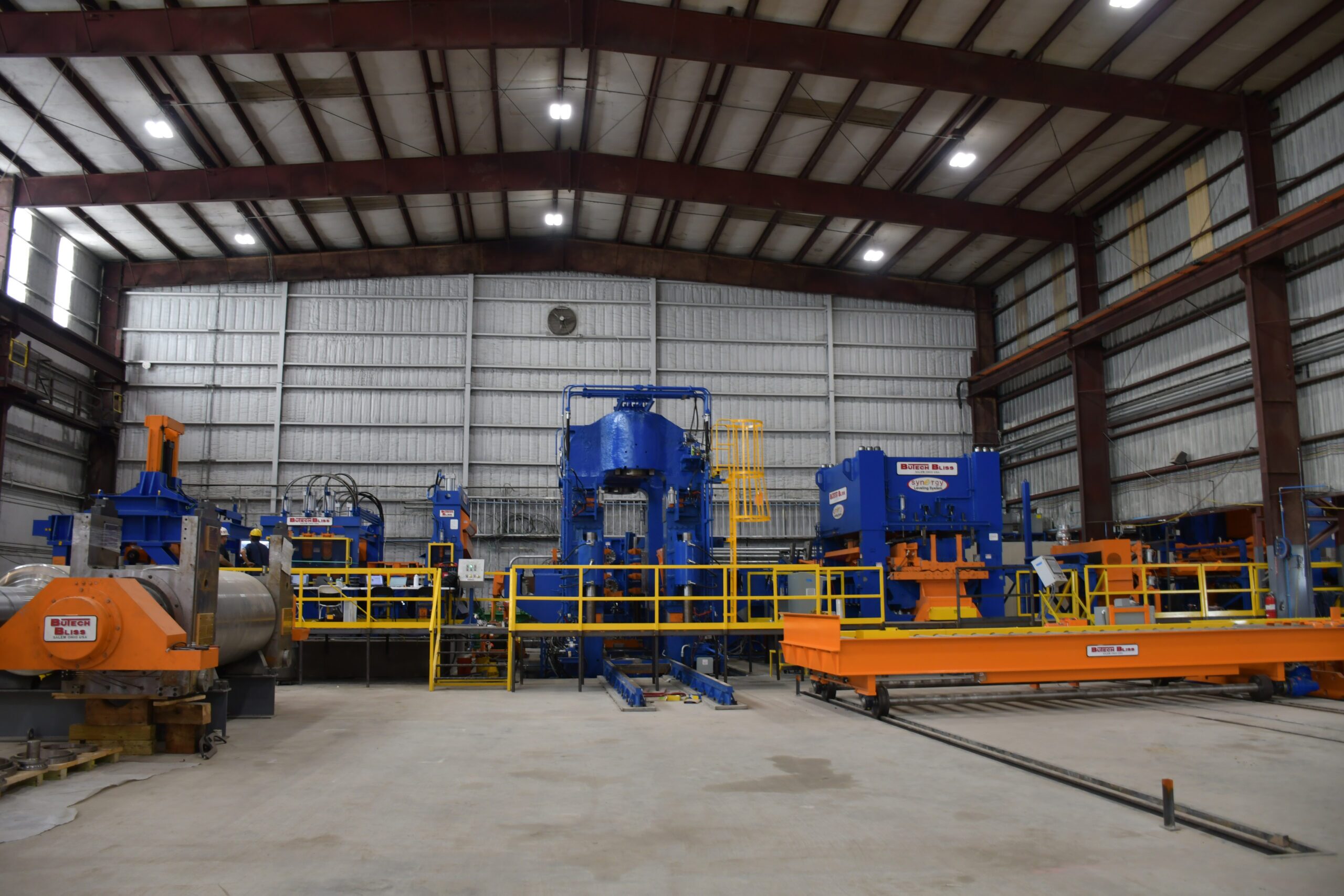
The temper mill system is a high production line with a rotary or flying shear. It includes levelers located after the mill to continue to correct the material. Temper pass steel is steel that passed through a set of rolls under pressure to improve flatness, surface finish, and mechanical properties.
The end product is high-quality steel that has reduced surface irregularities, enhanced surface texture, and minimal internal stresses. It will remain stable during welding, forming, or burning.
In addition to the new temper mill being installed in its Catoosa, OK facility, Norfolk Iron also has a temper mill in its Norfolk, NE facility.
Standard Cut-to-Length Line
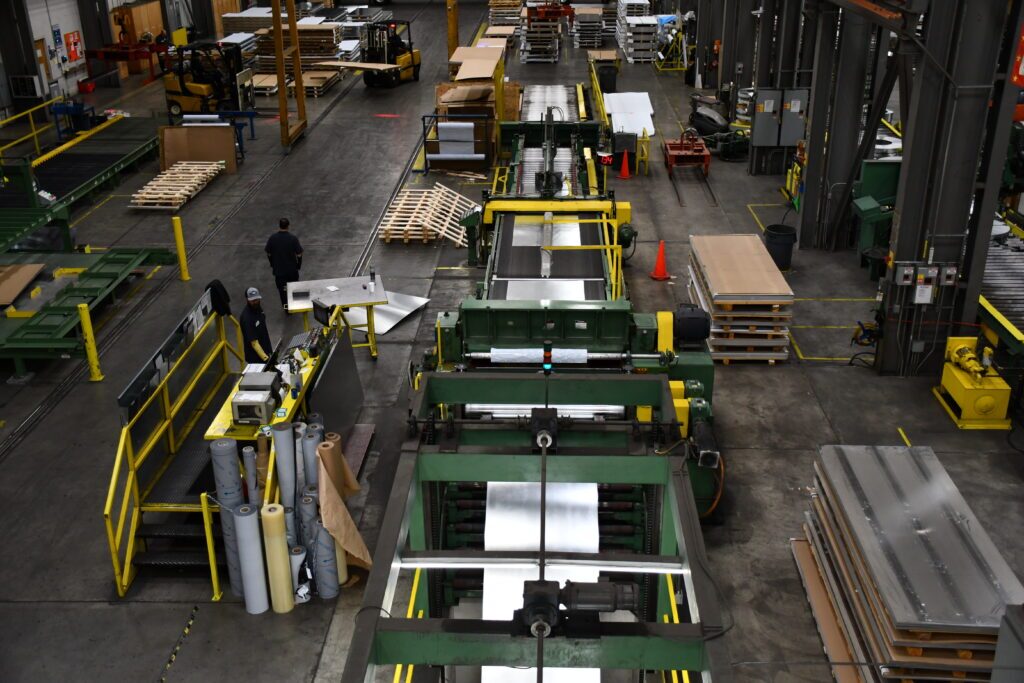
The standard cut-to-length line is a simpler system that levels and cuts previously processed steel coils to predetermined lengths without additional rolling or tempering. The basic process is comprised of unwinding the master coil, levelling the material, cutting, and then stacking and packaging the now cut sheets.
Norfolk Iron has cut-to-length lines located in the Brighton, CO, Monroe Twp., NJ, Garland, TX, Ogden, UT, and Windsor, CO facilities. These lines provide material to customers all across the U.S.
Stretcher Leveling Line
Stretcher leveling is a process that stretches the material beyond its yield point to remove the memory (spring back) of the coil. It improves dimensional accuracy and relieves residual stresses. After the material is stretched, it heads to a shear to be cut into sheets and packaged.
All three processes have their own unique benefits, but we are excited to have a new line that will provide material that has superior surface finish, better mechanical properties, and lower residual stress to our customers.
Each of our facilities offer different types of processing equipment. To learn more about the different processing capabilities Norfolk Iron has, visit our product and processing services page or contact your local sales representative to learn more.